A look behind the scenes
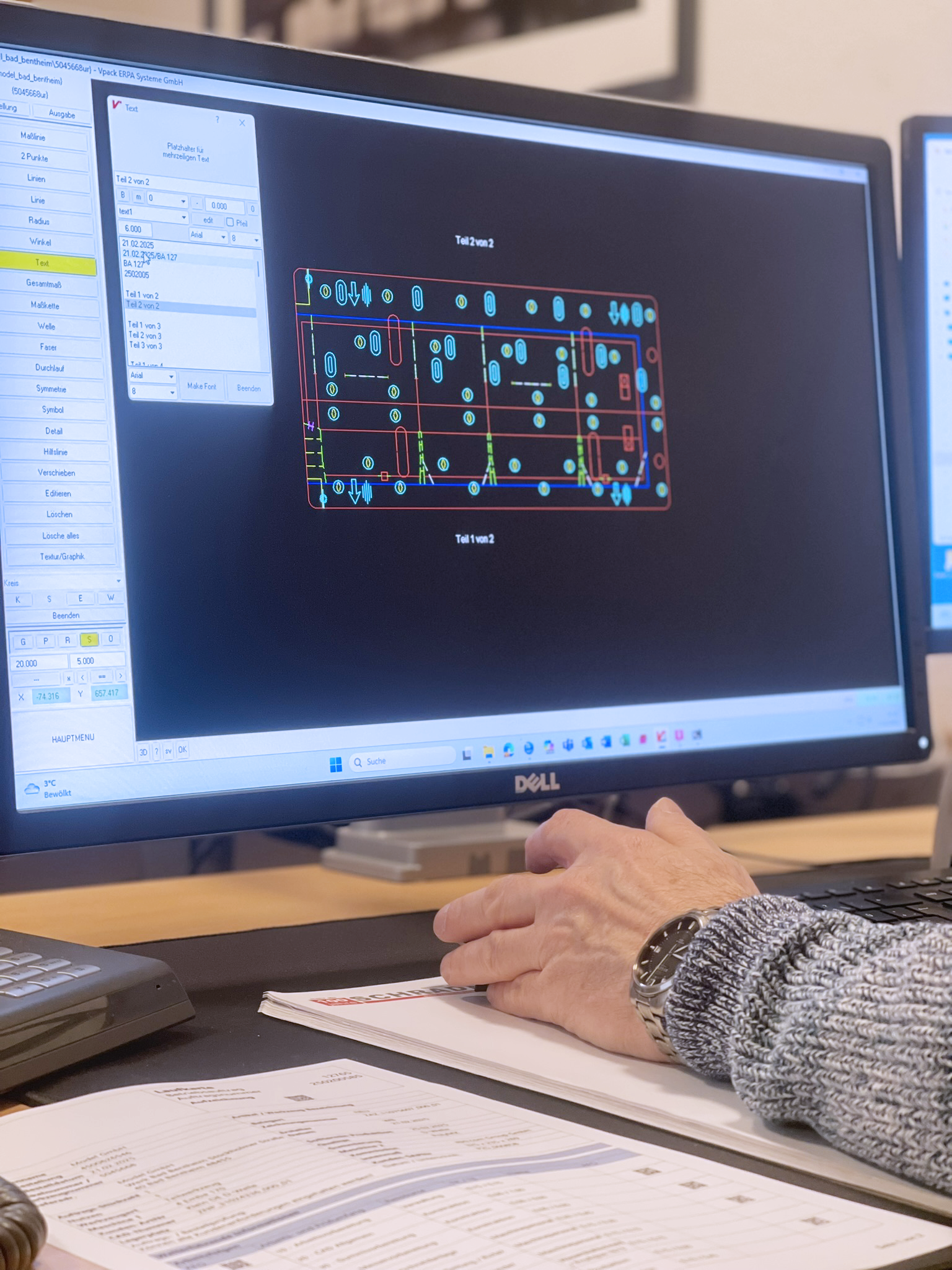
Order Intake and Work Preparation
After an order is received, it is recorded and a specific work card is created.
The electronically transmitted data is now prepared by our CAD staff.
After processing and inspection by another CAD team member, the completed dataset is sent to the machines.
Laser
The shaped wood is cut to size using the laser systems, and the contours for the packaging and waste removal are burned in.
Also, the mounting holes are countersunk, and the impact discs as well as the elongated slot plates are integrated.
The finished shaped wood is now inspected to ensure that the cutting widths for further processing have been correctly lasered.
Line Processing with Waterjet Cutter
On additional machines, the lines are pre-bent and the rubber coating for the respective areas is applied.
Despite the machine-prepared work processes, manual rework is required.
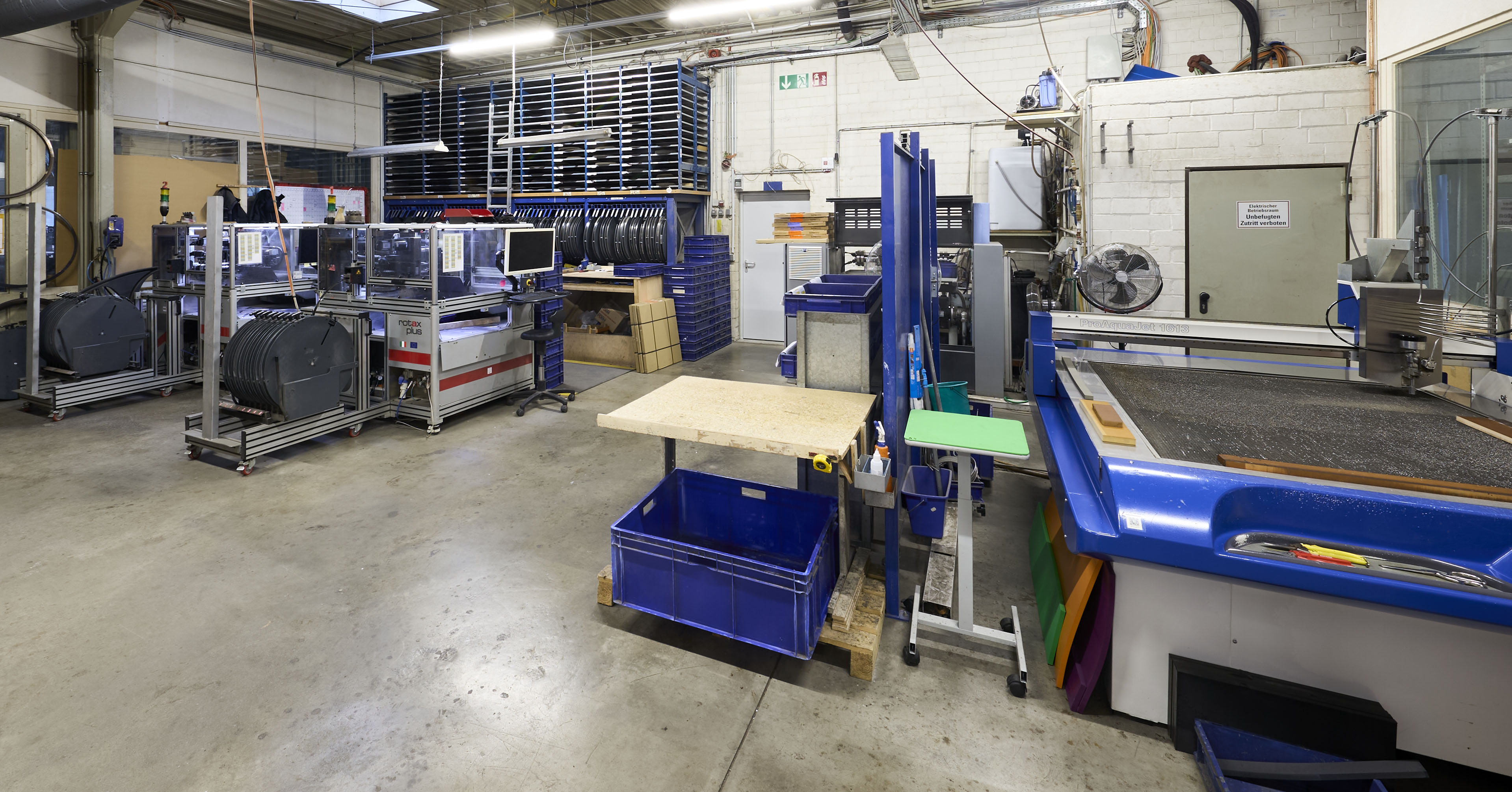
Manual Processing
The precise, artisanal construction of our stamping dies begins with incorporating and accurately adjusting the lines into the rotary blanks. This process requires the utmost care and a refined sense of touch from our employees. At the same time, it represents the most time-intensive step within the entire manufacturing process.
After completion, a foreman subjects the measured tool to a thorough quality inspection. Afterwards, it is handed over to the rubber coating department.
Rubber Coating
In this area, the previously machine-cut and manually applied rubber coating is applied to the tool.
Before the handover to the shipping department, a quality control check is carried out by our foremen.
Final Work Step Before Shipping
For full stamping dies with a diameter of 487 mm, we can perform die cutting operations up to a length of 2600 mm directly in-house.
After the final quality control, the stamping dies are carefully packaged and handed over to the freight carrier for delivery.